Machining
Recommendations
WHAT IS TOOLOX?
Toolox® is a modern quenched and tempered prehardened engineering and tool steel, delivered with measured and guaranteed mechanical properties. The basic idea is to save you time by delivering Toolox heat treated and ready to use. It provides you with lower costs, reduced risks and saves you valuable time in your production process due to its excellent machinability. This combined with the benefit of working with the hardest prehardened tool steel in the world gives you a simple to use material with a wide variety of uses.
Toolox is based on the same low carbon content as in Hardox® and Strenx®, but it is specially developed for tools and machine components working at high temperatures. It has excellent fatigue properties, and you can increase the surface hardness with nitriding or PVD coatings to gain more control over the service life of your tools or components.
In the information that follows, you will find our recommendations of tools to process Toolox. Similar tools from other suppliers might work, but here are the ones we have tested so far.
SHORTER LEAD TIME FROM CONCEPT TO PRODUCTION
1. Your customer has an idea
2. Manufacturing
3. Transport
4. Quenching and tempering
5. Adjusting
6. Production
DRILLING RECOMMENDATIONS
HSS DRILLS
Use only HSS drills when you have unstable machine conditions. If the machine conditions are good you can use different solid/brazed cemented carbide drill or drills with exchangeable heads.
Use an HSS-Co drill (8% Co) with a low helix angle and a robust core that can withstand high torques.
Individual holes can be drilled with an ordinary HSS drill. For a rational production, either a microalloyed (HSS-E) or a Cobalt alloyed (HSS-Co) drill is recommended.
METRIC (mm) |
Toolox 33 |
Toolox 40 |
Toolox 44 |
Vc m/min |
~ 15 |
~ 9 |
~ 7 |
Dc ( mm ) |
Feed rate ( mm/min and speed ( rpm ) |
5 |
0.10/950 |
0.05/570 |
0.05/445 |
10 |
0.10/475 |
0.10/290 |
0.09/220 |
15 |
0.16/325 |
0.16/190 |
0.15/150 |
20 |
0.23/235 |
0.22/150 |
0.20/110 |
25 |
0.30/195 |
0.28/110 |
0.25/90 |
30 |
0.35/165 |
0.35/90 |
0.30/75 |
*35 |
0.40/136 |
0.40/80 |
0.35/63 |
*40 |
0.45/119 |
0.45/70 |
0.40/55 |
US (in.) |
Toolox 33 |
Toolox 40 |
Toolox 44 |
Vc ft/min |
~ 50 |
~ 30 |
~ 23 |
Dc ( in ) |
Feed rate (in./min) and speed (rpm) |
0.197 |
0.004 |
0.002 |
0.002 |
0.394 |
0.004 |
0.004 |
0.004 |
0.591 |
0.006 |
0.006 |
0.006 |
0.787 |
0.009 |
0.009 |
0.008 |
0.984 |
0.012 |
0.011 |
0.010 |
1.181 |
0.014 |
0.014 |
0.012 |
1.378 |
0.016 |
0.0016 |
0.014 |
1.575 |
0.018 |
0.018 |
0.016 |
* WHEN USING A LARGE DRILL DIAMETER ( >30 MM), MAKE SURE THAT:
- The machine is large and stable enough to raise sectinal forces.
- The spindle has zero play.
- The workpiece is well clamped.
- Motor output is equal to or greater than 7.5 kW.
ADVICE TO REDUCE VIBRATIONS AND INCREASE THE LIFETIME OF THE DRILL
- Minimize the distances to the column and between to drill tip and the workpiece
- Don ́t use a longer drill than necessary
- Always use metal supports
- Clamp securely
- Use a solid and firm table
- Always use coolant
- Coolant mix 8-10 %
- Just before the drill breaks through, disengage the feed rate for a second. Otherwise, play/springback can snap the drill tip. Re-engage the feed rate after the play/springback stops.
SOLID CEMENTED CARBIDE DRILL
For stable machine conditions and with internal
coolant. Coolant mix 8-10 % for all drilling.
|
METRIC |
Toolox 33
65-90 |
Toolox 40
50-70 |
Toolox 44
40-65 |
Diameter (mm) |
Vc ( m/min) |
fn ( mm/rev ) |
min-max |
start value |
min-max |
start value |
min-max |
start value |
3.0 -5.0 |
0.08-0.15 |
0.10 |
0.06-0.12 |
0.08 |
0.06-0.11 |
0.07 |
5.01-10.0 |
0.09-0.16 |
0.12 |
0.08-0.15 |
0.11 |
0.08-0.13 |
0.10 |
10.01-15.0 |
0.16-0.22 |
0.18 |
0.14-0.20 |
0.16 |
0.12-0.18 |
0.15 |
15.01-20.0 |
0.22-0.28 |
0.25 |
0.16-0.24 |
0.20 |
0.16-0.20 |
0.18 |
*drilling 7x Dc, reduce the feed ~20 %
*drilling with external coolant ,reduce the speed and feed ~ 20 %
|
US |
Toolox 33
213-295 |
Toolox 40
164-230 |
Toolox 44
131-213 |
Diameter (in.) |
Vc (ft/min) |
fn (in./rev) |
min-max |
start value |
min-max |
start value |
min-max |
start value |
0.118-0.197 |
0.003-0.006 |
0.004 |
0.002-0.005 |
0.003 |
0.002-0.004 |
0.003 |
0.197-0.394 |
0.004-0.006 |
0.005 |
0.003-0.006 |
0.004 |
0.003-0.005 |
0.004 |
0.394-0.591 |
0.006-0.009 |
0.007 |
0.006-0.008 |
0.006 |
0.005-0.007 |
0.006 |
0.591-0.787 |
0.009-0.011 |
0.0010 |
0.006-0.009 |
0.008 |
0.006-0.008 |
0.008 |
DRILLS WITH EXCHANGEABLE DRILL HEADS OR
BRAZED CEMENTED CARBIDE DRILL
For stable machine conditions and with internal coolant.
|
METRIC |
Toolox 33
50-80 |
Toolox 40
50-65 |
Toolox 44
40-60 |
Diameter (mm) |
Vc ( m/min ) |
fn ( mm/rev ) |
min-max |
start value |
min-max |
start value |
min-max |
start value |
7.5-12.0 |
0.10-0.16 |
0.13 |
0.08-0.15 |
0.12 |
0.08-0.14 |
0.11 |
12.01-20.0 |
0.15-0.23 |
0.20 |
0.12-0.22 |
0.17 |
0.12-0.20 |
0.15 |
20.01-25.0 |
0.18-0.27 |
0.22 |
0.15-0.25 |
0.19 |
0.14-0.22 |
0.17 |
25.01-30.0 |
0.20-0.30 |
0.24 |
0.17-0.27 |
0.21 |
0.16-0.25 |
0.19 |
*Drilling with 25-30xD reduces the Feed rate by ~15-20 %
*The recommendation is to have at least 25 bar pressure on the waterpump.
|
US |
Toolox 33
164-262 |
Toolox 40
164-213 |
Toolox 44
131-197 |
Diameter (in.) |
Vc (ft/min) |
fn (in./rev) |
min-max |
start value |
min-max |
start value |
min-max |
start value |
0.295-0.472 |
0.004-0.006 |
0.005 |
0.003-0.006 |
0.005 |
0.003-0.006 |
0.004 |
0.473-0.787 |
0.006-0.009 |
0.008 |
0.005-0.009 |
0.007 |
0.005-0.008 |
0.006 |
0.788-0.984 |
0.007-0.011 |
0.009 |
0.006-0.010 |
0.007 |
0.006-0.009 |
0.007 |
0.788-0.984 |
0.008-0.012 |
0.009 |
0.007-0.011 |
0.008 |
0.006-0.010 |
0.007 |
LONG HOLE DRILLING WITH 16-20xD
For stable machine conditions and with internal coolant.
|
METRIC |
Toolox 33
50-70 |
Toolox 40
50-65 |
Toolox 44
40-60 |
Diameter (mm) |
Vc ( m/min ) |
fn ( mm/rev ) |
min-max |
start value |
min-max |
start value |
min-max |
start value |
6.0 |
0.12-0.16 |
0.14 |
0.10-0.15 |
0.12 |
0.08-0.14 |
0.11 |
8.0 |
0.14-0.20 |
0.16 |
0.11-0.18 |
0.14 |
0.10-0.18 |
0.13 |
10.0 |
0.17-0.24 |
0.19 |
0.13-0.22 |
0.16 |
0.12-0.21 |
0.15 |
12.0 |
0.18-0.26 |
0.20 |
0.15-0.24 |
0.18 |
0.14-0.23 |
0.17 |
* The cutting data on this page has been formulated in cooperation with Seco Tools.
|
US |
Toolox 33
164-262 |
Toolox 40
164-213 |
Toolox 44
131-197 |
Diameter (in.) |
Vc (ft/min) |
fn (in./rev) |
min-max |
start value |
min-max |
start value |
min-max |
start value |
0.236 |
0.005-0.006 |
0.006 |
0.004-0.006 |
0.005 |
0.003-0.006 |
0.004 |
0.315 |
0.006-0.008 |
0.006 |
0.004-0.007 |
0.006 |
0.004-0.007 |
0.005 |
0.394 |
0.007-0.009 |
0.007 |
0.005-0.009 |
0.006 |
0.005-0.008 |
0.006 |
0.472 |
0.007-0.010 |
0.008 |
0.006-0.009 |
0.007 |
0.006-0.009 |
0.007 |
MILLING RECOMMENDATIONS
CLAMPING
Toolox has a very low level of residual stresses. To get the full effect make sure to use deformation-free clamping. If blanks are gas cut, mill off 5-10mm from the gas-cut edge to get a blank free from residual stresses.
The machinability of Toolox has been improved. During milling you will notice it because the chips produced are very bluish. We have modified the carbide morphology as compared to traditional tool steels, using less carbon in Toolox. Therefore, the heat generated during milling is transferred into the chip and not into the cutting edge/workpiece.
MILLING ADVICE
- Position the cutter off-center (to the left) to achieve a thicker chip at the entry and to avoid thick chip on the exit.
- Avoid cutting through the center line of the cutter, because this can generate vibration.
- Always use down milling (climb millIng).
- The recommendation is that the radial engagement of the cutter (ae) should be 25 or 75-80% of the diameter.
If you enter the workpiece with the roll-into-cut method, the chip thickness on the exit is always zero, and it will help to give a longer tool life.
Roll-into-cut method
Wear after 800 passes
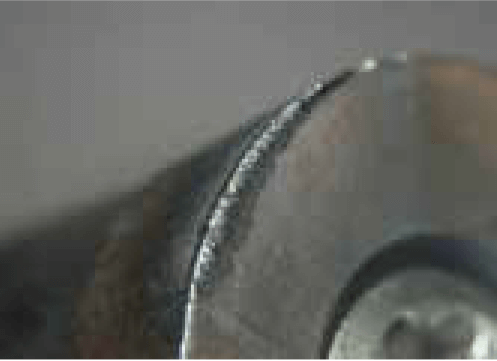
Straight into the workpiece
Wear after 390 passes
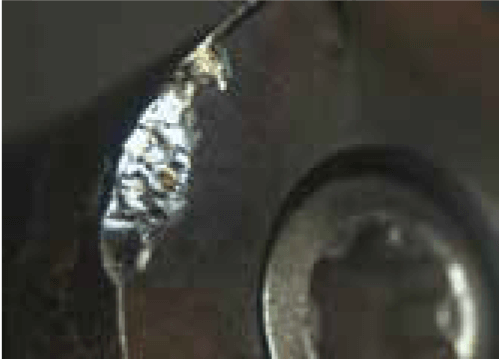
Roll-into-cut method
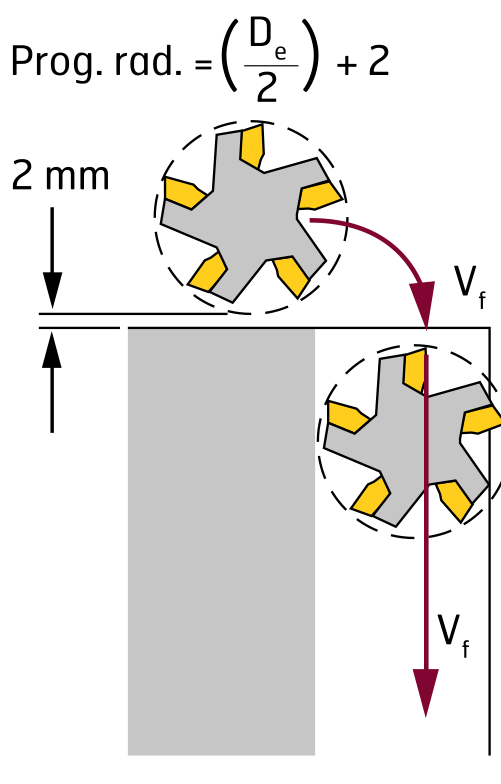
INSERT GRADES FOR MILLING
P |
ISO |
ANSI |
|
01 |
C8 |
|
10 |
C7 |
|
20 |
|
|
30 |
C6 |
|
40 |
|
|
50 |
C5 |
|
M |
10 |
|
|
20 |
|
|
30 |
|
|
40 |
|
|
K |
01 |
C4 |
|
10 |
C3 |
|
20 |
C2 |
|
30 |
C1 |
|
40 |
|
|
H |
01 |
C4 |
|
10 |
C3 |
|
20 |
C2 |
|
30 |
C1 |
|
Wear resistance
Toughness
P ISO P= Steel
M ISO M= Stainless steel
K ISO K= Cast iron
K ISO H= Hardened stee
* Example insert grade 1030.
“The last 2 numbers in the insert grade indicate where in this scale the insert belongs, if the insert has wear or toughness resistance.“
INSERT GEOMETRY
The macro geometry affects many parameters in the cutting process. An insert with a strong cutting edge can work at higher loads, but it will also generate higher cutting forces, consume more power and generate more heat.
Geometry |
Parameter |
L |
M |
N |
Edge strength |
 |
Cutting forces |
Power consumption |
Max chip thickness |
Heat generated |
* Use insert grade P 30-50 with light cutting geometry and a coarse - pitch cutter if the machine power is low and with unstable machine conditions.
TURNING RECOMMENDATIONS
he cutting data recommendations below are applicable to tough cemented carbide grades. These are necessary for operations in which impact may occur, such as when turning plate with gas-cut edges.
METRIC |
Vc (m/min) |
Toolox 33
150-200 |
Toolox 40
90-140 |
Toolox 44
80-120 |
Feed rate (fn) |
min-max |
min-max |
min-max |
Insert grade P25 (mm/rev) |
0.20-0.40 |
0.20-0.40 |
0.20-0.40 |
At higher Feed rate , lower the cutting speed
US |
Vc (ft/min) |
Toolox 33
492-656 |
Toolox 40
295-459 |
Toolox 44
262-394 |
Feed rate (fn) |
min-max |
min-max |
min-max |
Insert grade P25 (in./rev) |
0.008-0.016 |
0.008-0.016 |
0.008-0.016 |
Formulas for turning |
Definitions |
 |
Vc = cutting speed (m/min, ft/min)
n = speed (rpm)
fn = Feed rate (mm/rev, in./rev)
vf = Feed rate (mm/min, in./min)
d = workpiece Ø
π = 3,14 |
FACE MILLING RECOMMENDATION
Round inserts have strong cutting edges and are good to use when the surface has holes and cavities etc
METRIC |
Recommendation for average machine conditions with a 45°setting angle |
Vc (m/min) |
Toolox 33
180-220 |
Toolox 40
90-140 |
Toolox 44
120-160 |
Feed rate (fz) |
min-max |
start value |
min-max |
start value |
min-max |
start value |
Insert grade P30 |
0.15-0.35 |
0.25 |
0.15-0.35 |
0.25 |
0.15-0.35 |
0.25 |
US |
Recommendation for average machine conditions with a 45°setting angle |
Vc (ft/min) |
Toolox 33
591-722 |
Toolox 40
295-459 |
Toolox 44
394-525 |
Feed rate (fz) |
min-max |
start value |
min-max |
start value |
min-max |
start value |
Insert grade P30 |
0.006-0.014 |
0.010 |
0.006-0.014 |
0.010 |
0.006-0.014 |
0.010 |
METRIC |
Recommendation for average machine conditions with round inserts |
Vc (m/min) |
Toolox 33
180-220 |
Toolox 40
170-210 |
Toolox 44
140-180 |
Feed rate (fz) |
min-max |
start value |
min-max |
start value |
min-max |
start value |
Insert grade P30 |
0.10-0.25 |
0.15 |
0.10-0.25 |
0.15 |
0.10-0.25 |
0.15 |
US |
Recommendation for average machine conditions with round inserts |
Vc (ft/min) |
Toolox 33
591-722 |
Toolox 40
558-689 |
Toolox 44
459-591 |
Feed rate (fz) |
min-max |
start value |
min-max |
start value |
min-max |
start value |
Insert grade P30 |
0.000 -0.001 |
0.001 |
0.000-0.001 |
0.001 |
0.000-0.001 |
0.001 |
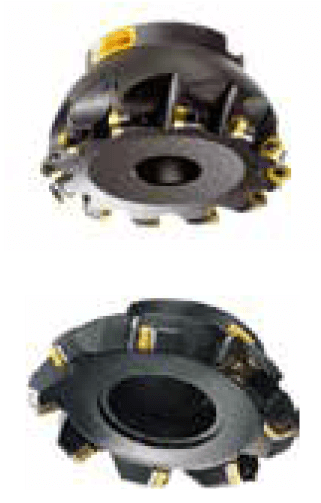
SHOULDER MILLING RECOMMENDATION
METRIC |
Recommendation for average machine conditions with a 90°setting angle |
Vc (m/min) |
Toolox 33
180-220 |
Toolox 40
140-180 |
Toolox 44
120-160 |
Feed rate (fz) |
min-max |
start value |
min-max |
start value |
min-max |
start value |
Insert grade P30 |
0.12-0.25 |
0.17 |
0.12-0.25 |
0.17 |
0.12-0.25 |
0.17 |
US |
Recommendation for average machine conditions with a 90°setting angle |
Vc (ft/min) |
Toolox 33
591-722 |
Toolox 40
459-591 |
Toolox 44
394-525 |
Feed rate (fz) |
min-max |
start value |
min-max |
start value |
min-max |
start value |
Insert grade P30 |
0.005-0.010 |
0.007 |
0.005-0.010 |
0.007 |
0.005-0.010 |
0.007 |
END MILLING RECOMMENDATION FOR SOLID CEMENTED CARBIDE TOOL
METRIC |
Slot milling recommendation |
Shoulder milling recommendation |
|
Toolox 33 |
Toolox 40 |
Toolox 44 |
Toolox 33 |
Toolox 40 |
Toolox 44 |
Vc (m/min) |
85-110 |
75-100 |
70-95 |
200-230 |
180-210 |
160-190 |
Feed rate (fz) |
min-max |
min-max |
min-max |
min-max |
min-max |
min-max |
Diameter |
3.0-6.0 |
0.01-0.03 |
0.01-0.03 |
0.01-0.03 |
0.02-0.05 |
0.02-0.04 |
0.02-0.04 |
8.0-12.0 |
0.04-0.07 |
0.03-0.06 |
0.03-0.06 |
0.07-0.10 |
0.06-0.09 |
0.06-0.09 |
14.0-20.0 |
0.07-0.10 |
0.06-0.09 |
0.06-0.08 |
0.10-0.14 |
0.10-0.13 |
0.10-0.12 |
* If possible, use only compressed air to remove the chip and use weldon chuck for tool over Ø 10.
US |
Slot milling recommendation |
Shoulder milling recommendation |
|
Toolox 33 |
Toolox 40 |
Toolox 44 |
Toolox 33 |
Toolox 40 |
Toolox 44 |
Vc (ft/min) |
279-361 |
246-328 |
230-312 |
656-755 |
591-689 |
525-623 |
Feed rate (fz) |
min-max |
min-max |
min-max |
min-max |
min-max |
min-max |
Diameter |
0.118-0.236 |
0.000-0.001 |
0.000-0.001 |
0.000-0.001 |
0.001-0.002 |
0.001-0.002 |
0.001-0.002 |
0.315-0.472 |
0.002-0.003 |
0.001-0.002 |
0.001-0.002 |
00.003-0.004 |
0.002-0.004 |
0.002-0.004 |
0.551-0.787 |
0.003-0.004 |
0.002-0.004 |
0.002-0.003 |
0.004-0.006 |
0.004-0.005 |
0.004-0.005 |
Slot milling advice
ap (depth of cut) max 0.5 x D
Shoulder milling advice
ap (use the whole cutting length)
ae (radial depth of cut) max 0.1 x D
TAPPING RECOMMENDATIONS
With the correct tools you can perform all tapping/thread milling operations using all Toolox grades. We recommend four-flute taps, which can withstand the very high torque that occurs during tapping in hard materials. If is not critical, the drilled hole can be 3% larger than standard. This will increase the lifetime of the tap.
* Thread oil or thread paste is recommended as lubricant.
METRIC |
Vc (m/min |
Toolox 33
7-10 |
Toolox 40
4-9 |
Toolox 44
3-5 |
US |
Vc (ft/min) |
Toolox 33
23-33 |
Toolox 40
13-30 |
Toolox 44
10-16 |
Size |
Speed ( rpm ) |
Speed ( rpm ) |
Speed ( rpm ) |
M5 |
445-635 |
255-570 |
190-320 |
M6 |
370-530 |
210-475 |
160-265 |
M8 |
270-400 |
160-360 |
120-200 |
M10 |
220-320 |
125-285 |
95-160 |
M12 |
185-265 |
105-240 |
80-130 |
M16 |
140-200 |
80-180 |
60-100 |
M20 |
110-160 |
60-140 |
45-80 |
* We recommend thread milling for thread below M5 especially in Toolox 40 and 44.
METRIC |
|
Toolox 33 |
Toolox 40 |
Toolox 44 |
Vc (m/min |
80-110 |
60-80 |
50-70 |
fz mm |
0.03-0.06 |
0.02-0.05 |
0.02-0.05 |
* To manage thread milling, a CNC machine is necessary and the thread should be made in 2 passes.
US |
|
Toolox 33 |
Toolox 40 |
Toolox 44 |
Vc (ft/min) |
263-361 |
197-263 |
164-230 |
fz (in.) |
0.001-0.002 |
0.001-0.002 |
0.001-0.002 |
COUNTERSINKING & COUNTERBORING
Countersinking and counterboring are best performed using tools that have replaceable inserts. Always use a revolving pilot and use coolant.
METRIC |
Vc ( m/min ) |
Toolox 33
40 - 80 |
Toolox 40
25 - 70 |
Toolox 33
20 - 50 |
Feed rate (mm/rev) |
0.10-0.20 |
0.10-0.20 |
0.10-0.20 |
Dc (mm) |
Speed ( rpm ) |
19 |
670-1340 |
420-1175 |
335-840 |
24 |
530-1060 |
330-930 |
265-665 |
34 |
375-750 |
235-655 |
185-470 |
42 |
300-600 |
190-530 |
150-380 |
57 |
225-440 |
140-390 |
110-280 |
* Reduce the cutting data by about 30 % in countersinking.
US |
Vc (ft/min) |
Toolox 33
131-262 |
Toolox 40
82-230 |
Toolox 33
66-164 |
Feed rate (mm/rev) |
0.004-0.008 |
0.004-0.008 |
0.004-0.008 |
Dc (in.) |
Speed ( rpm ) |
0.748 |
670-1340 |
420-1175 |
335-840 |
0.945 |
530-1060 |
330-930 |
265-665 |
1.339 |
375-750 |
235-655 |
185-470 |
1.654 |
300-600 |
190-530 |
150-380 |
2.244 |
225-440 |
140-390 |
110-280 |
RESULTS FROM OUR OWN TESTS
MACHINE INFO
VMC FADAL 4020 HT modell 1997
Spindle type ISO 40 tape
Through spindle coolant
Spindle speed max 10,000 rpm
Effect on the spindle motor 16.8 kw
Torque 303 Nm.
Toolox 33 |
Tool |
Ø |
Vc |
f |
ap |
ae |
runtime |
Shoulder milling |
Coromill 490 |
50 mm |
180 m |
0.17 mm |
4 mm |
13 mm |
196 min |
|
|
1.969 in. |
591 ft. |
0.007 in. |
0.157 in. |
0.512 in. |
196 min |
Runtime 132 min |
Runtime 196 min |
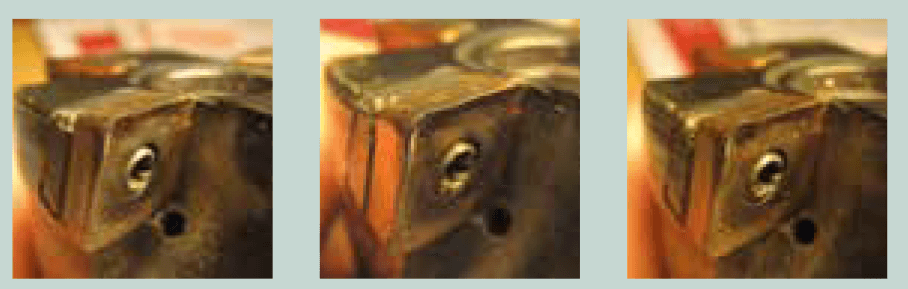 |
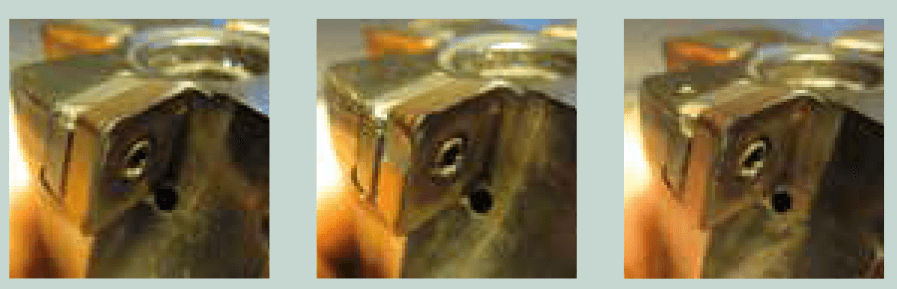 |
Toolox 40 |
Tool |
Ø |
Vc |
f |
ap |
ae |
runtime |
Face milling |
Coromill 490 |
100 mm |
160 m |
0.25 mm |
2 mm |
68 mm |
43 min |
|
|
3.937 in. |
525 ft. |
0.010 in. |
0.079 in. |
2.677 in. |
43 min |
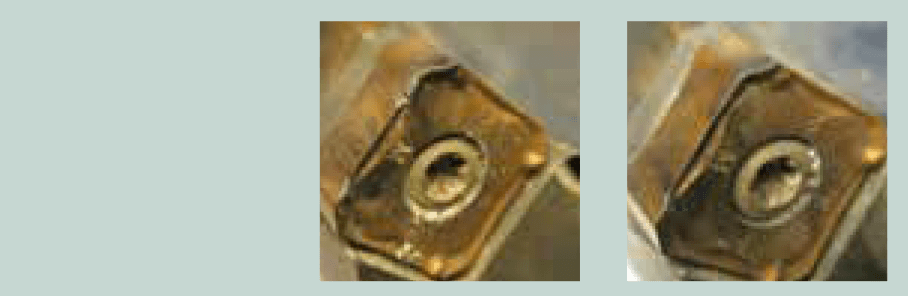 |
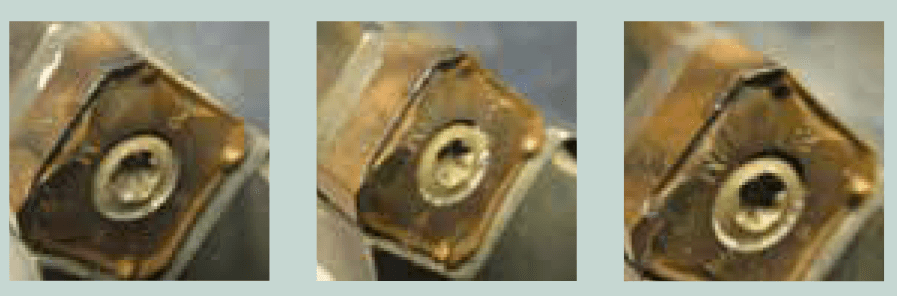 |
Toolox 44 |
Tool |
Ø |
Vc |
f |
ap |
ae |
runtime |
Face milling |
Coromill 345 |
100 mm |
150 m |
0.25 mm |
2 mm |
61 mm |
32 min |
|
|
3.937 in. |
492 ft. |
0.010 in. |
0.079 in. |
2.402 in. |
32 min |
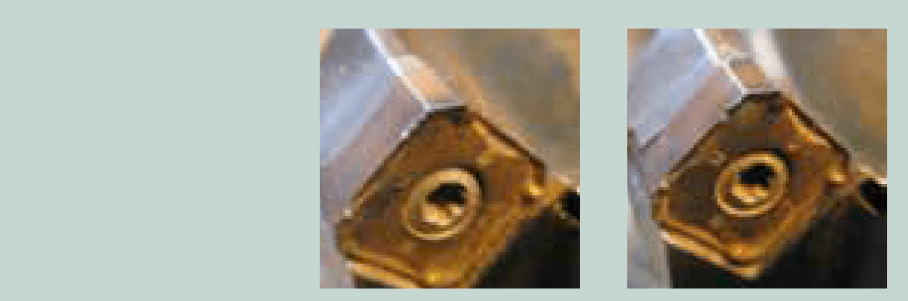 |
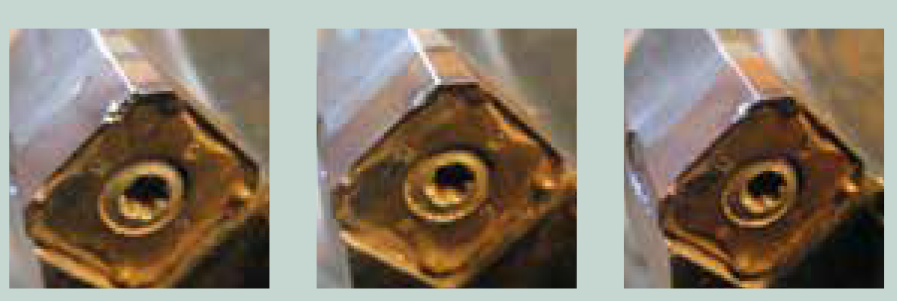 |
Toolox 44 |
Tool |
Ø |
Vc |
f |
ap |
ae |
runtime |
Shoulder milling |
End milling |
16 mm |
180 m |
0.12 mm |
34 mm |
1.6 mm |
103 min |
|
|
0.630 in |
591 ft. |
0.005 in |
1.339 in. |
0.063 in. |
103 min |
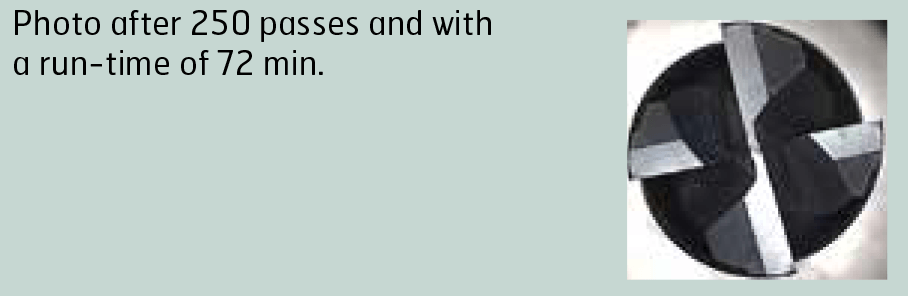 |
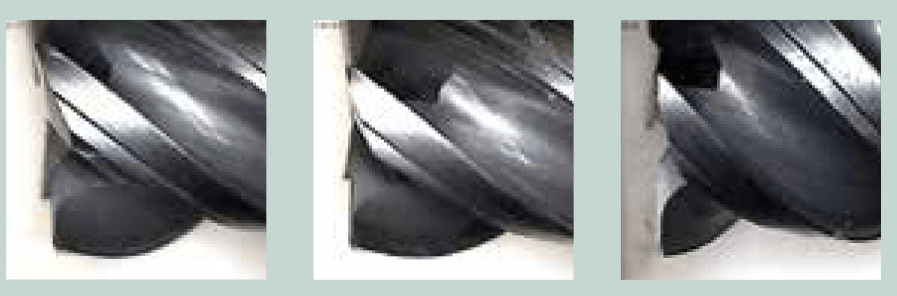 |
Toolox 33 |
Tool |
Ø |
Vc |
fn |
total |
drill depth |
coolant flow |
Drilling/ blind holes |
Corodrill 840 |
6.8 mm |
80 m |
0.12 mm |
1105 |
23 mm |
1.9 l/min |
|
|
0.630 in. |
591 ft. |
0.005 in. |
|
0.906 in. |
0.502 GPM |
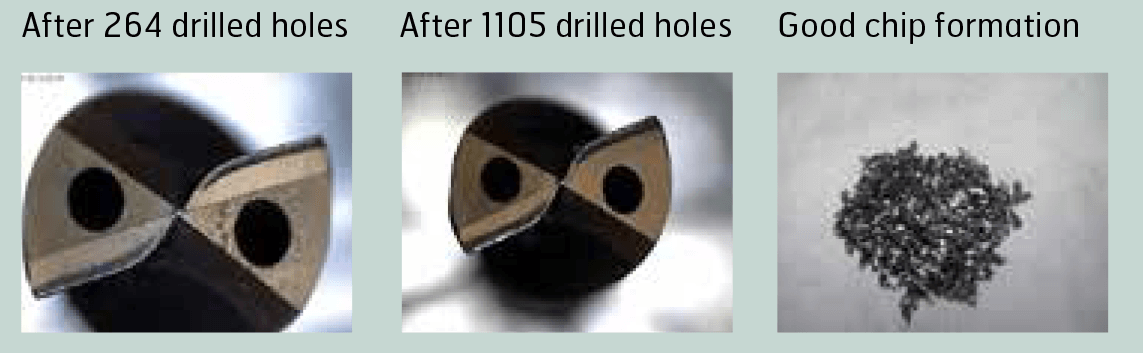 |
|
Toolox 40 |
Tool |
Ø |
Vc |
fn |
total |
drill depth |
coolant flow |
Drilling/ blind holes |
Seco Feedmax |
4.3 mm |
70 m |
0.12 mm |
608 |
16 mm |
0.2 l/min |
|
|
0.169 in. |
230 ft. |
0.005 in. |
|
0.630 in. |
0.053 GPM |
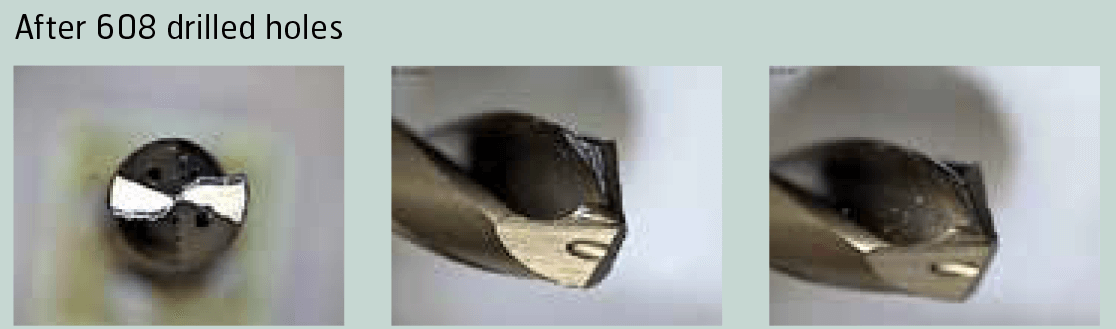 |
|
Toolox 44 |
Tool |
Ø |
Vc |
fn |
total |
drill depth |
coolant flow |
Drilling/ blind holes |
Seco Feedmax |
4.3 mm |
60 m |
0.06 mm |
438 |
15 mm |
0.21 l/min |
|
|
0.169 in. |
197 ft. |
0.002 in. |
|
0.591 in. |
0.053 GPM |
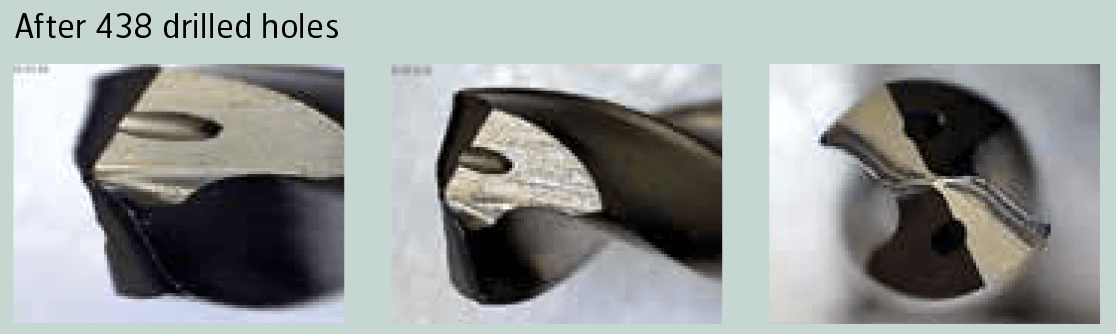 |
|
Toolox 40 |
Tool |
drill Ø |
Ø |
Vc |
thread
depth |
Total |
Tapping / blind holes |
Manigley 131/3 DUO |
4.3 mm |
M5 |
11 m |
12 mm |
330 |
|
|
0.169 in. |
M5 |
36 ft. |
0.472 in. |
330 |
Toolox 40 |
Tool |
drill Ø |
Ø |
Vc |
thread
depth |
Total |
Tapping / blind holes |
Manigley 131/3 DUO |
10.2 mm |
M12 |
8 m |
24 mm |
217 |
|
|
0.402 in. |
M12 |
26 ft. |
0.945 in. |
217 |
Toolox 44 |
Tool |
drill Ø |
Ø |
Vc |
thread
depth |
Total |
Tapping / blind holes |
Manigley 131/3 DUO |
4.3 mm |
M5 |
3 m |
10 mm |
183 |
|
|
0.169 in. |
M5 |
10 ft. |
0.394 in. |
183 |
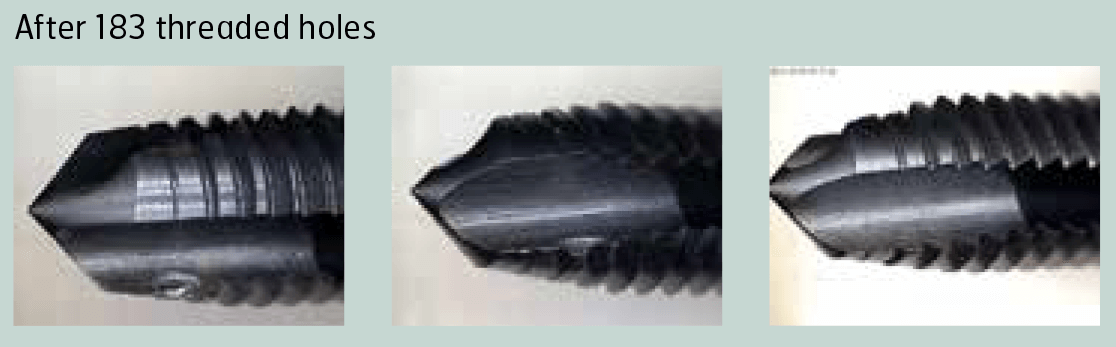 |
|
Toolox 40 |
Tool |
drill Ø |
Ø |
Vc |
thread
depth |
Total |
Tapping / blind holes |
Manigley 131/3 DUO |
14.2 mm |
M16 |
6 m |
25 mm |
276 |
|
|
0.560 in. |
M16 |
20 ft. |
0.984 in. |
276 |
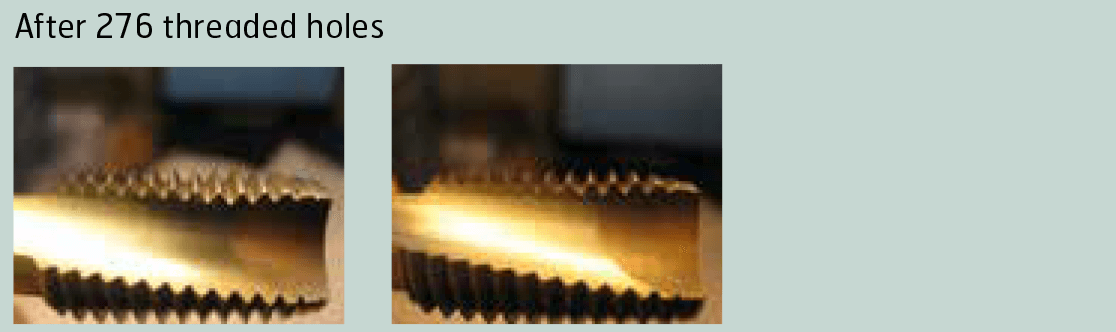 |
|
TOOL RECOMMENDATIONS FOR TOOLOX
DRILLING IN TOOLOX
Tool name |
Article No. |
Diameter range |
Seco
Feedmax |
* SD203A-12.0-36-12R1 |
2.0-20.0 mm
(0.079-0.787 in.) |
Tool name |
Article No. |
Diameter range |
Seco
Feedmax |
* SD216A-12.0-180-12R1 |
3.0-14.10 mm
(0.118-0.555 in.) |
Long holes drilling with 16-20xD
Solid cemented carbide drill
Supplier: Seco
Sweden
www.secotools.com
Tool name |
Article No. |
Diameter range |
Cordrill R840
Delta C |
R840-xxxx-30-A1A |
3.0-20.0 mm
(0.118-0.787 in.) |
Tool name |
Article No. |
Diameter range |
Chamdrill |
* SD103-12.00-40-16R7 |
0.0-25.99 mm
(0.394-1.023 in.) |
Drill with exchangeable drill heads
Drill heads grade: P
Supplier: Seco
Sweden
www.secotools.com
Tool name |
Article No. |
Diameter range |
Chamdrill |
DCM xxx-xxx-xxA-xx.xx |
7.5-25.9 mm
(0.295-1.020 in.) |
Drill with exchangeable drill heads
Drill heads grade: IC908
Supplier: Iscar
Israel
www.iscar.com
Tool name |
Article No. |
Diameter range |
HSS -E Co 8 Taper
Shank Drills, WN
103 |
832xxxxx |
8.0-40.0 mm
(0.315-1.575 in.) |
High-speed steel drill alloyed with
8 % cobalt (HSS-Co 8 %)
Supplier: Alpen-MayKestag
Austria
www.alpenmaykestag.com
TAPPING IN TOOLOX
Tap for blind holes
Tool name |
Article No. |
Diameter range |
1641 TC |
1641TC Mxx |
18.0-75.0 mm
(0.709-2.953 in.) |
HSS-P tap with TiCN coating
Supplier: Yamawa
Sweden
www.yamawa.eu
Tap for through holes
Tool name |
Article No. |
Diameter range |
105/4 DUO |
433xx |
20.5-60.0 mm
(0.807-2.362 in.) |
HSSE-PM tap with TiCN coating
Supplier: Manigley
Switzerland
www.manigley.ch
Tap for blind holes
Tool name |
Article No. |
Diameter range |
131/3 DUO |
433xx |
3.0-25.0 mm
(0.118-0.984 in.) |
HSSE-PM tap with TiCN coating
Supplier: Manigley
Switzerland
www.manigley.ch
Tap for blind holes
Tool name |
Article No. |
Diameter range |
Rekord 1D-TI-TiCN |
B0459601.xxxx |
M3-M10 |
Rekord 2D-TI-TiCN |
C0459601.xxxx |
M12-M24 |
Tap for through holes
Tool name |
Article No. |
Diameter range |
Rekord 1C-Ti-TiCN |
B0309601.xxxx |
M3-M10 |
Rekord 2C-Ti-TiCN |
C0309601.xxxx |
M12-M24 |
THREAD MILLING IN TOOLOX
Tool name |
Article No. |
Diameter range |
GSF-VHM 2xD
IKZ-HB TiCN |
GSF333106xxxx |
M3-M16 |
Solid carbide thread milling cutter
with TiCN coating
Supplier: Emuge Franken
Germany
www.emuge.de/english
Tool name |
Article No. |
Diameter range |
Solid carbide
thread mill |
NBxxxxxCxx
x.xISO AC |
M2-M42 |
Solid carbide thread milling
cutter with TiAlCN coating
Supplier: SmiCut
Sweden
www.smicut.se
COUNTERBORING IN TOOLOX
Use counterbore with indexable inserts that always have a grade number ending in H
Tool name |
Article No. |
Diameter range |
WHV counterbore |
XWHV-xx.x |
18.0-75.0 mm
(0.709-2.953 in.) |
COUNTERSINKING IN TOOLOX
Use countersink with indexable inserts that always have a grade number ending in H
Tool name |
Article No. |
Diameter range |
KV countersink |
xKV9-xx.x |
20.5-60.0 mm
(0.807-2.362 in.) |
END MILLING IN TOOLOX
Tool name |
Article No. |
Diameter range |
KV countersink |
xKV9-xx.x |
20.5-60.0 mm
(0.807-2.362 in.) |
Solid end milling cutter with Siron-A coating
Supplier: Seco
Sweden
www.secotools.com
MILLING WITH INSERT IN TOOLOX
Tool name |
Article No. |
Diameter range |
Coromill 345 |
345-xxxxxx-13x |
40-250 mm
(1.575-9.843 in.) |
Tool name |
Article No. |
Diameter range |
Coromill 300 |
R300-xxxxxx-xxx |
10-200 mm
0.394-7.874 in.) |
Tool name |
Article No. |
Diameter range |
Coromill 490 |
490-xxxxx-xxx |
20-250 mm
(0.787-9.843 in.) |
Tool name |
Article No. |
Diameter range |
Coromill 490 |
490-xxxxx-xxx |
20-250 mm
(0.787-9.843 in.) |
INSERT GRADE IN TOOLOX
Tool name |
Article No. |
Insert grade |
Insert
geometry |
Coromill 300 |
R300-xxxxx-Px |
1010 |
L-M-H |
R300-xxxxx-Px |
1030 |
L-M-H |
Coromill 345 |
345R-1305x-Px |
1010 |
L-M-H |
345R-1305x-Px |
1030 |
L-M-H |
Coromill 490 |
490R-xxxxxxx-Px |
1010 |
L-M |
490R-xxxxxxx-Px |
1030 |
L-M-H |
Use insert grade P1030 for average machine conditions. In very stable machine conditions and with a rigid set-up, insert grade P1010 is more suitable, especially in Toolox 40 and 44. Then you can increase the cutting speed by approximately 20-30%.
Supplier: Sandvik Coromant AB
Sweden
www.sandvik.coromant.com 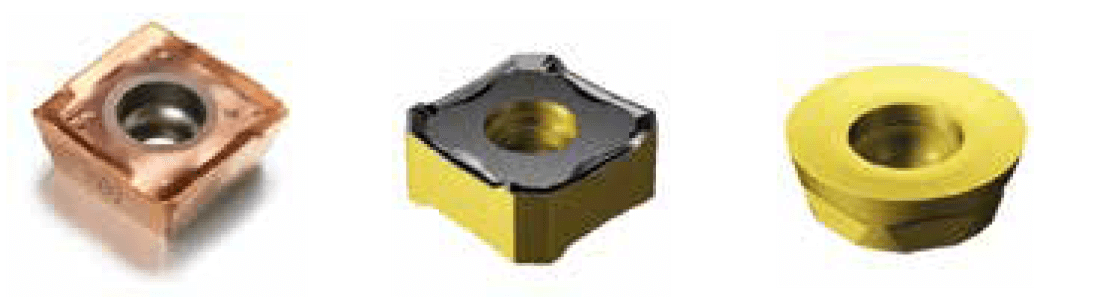
APLICATION AREAS
MOULDS
COLD WORK

HOT WORK
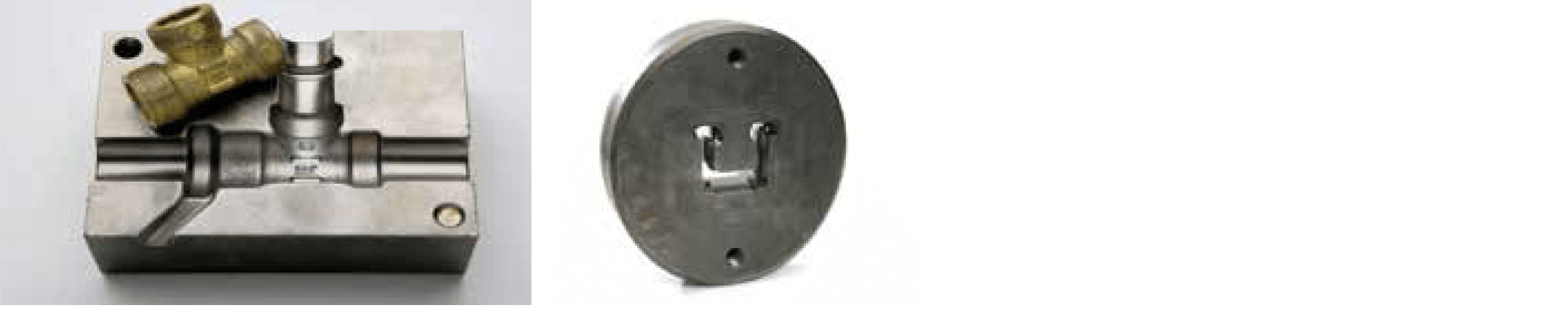
MACHINE COMPONENTS
